About AFDEX
Currently, AFDEX is theoretically based on the rigid- or elasto-thermoviscoplastic finite element method.
There are a number of modules. AFDEX 2D and AFDEX 2D/DIE use quadrilateral finite elements.
AFDEX 3D, AFDEX 3D/OPEN, and AFDEX 3D/DIE employ tetrahedral elements.
AFDEX 2D/DIE and AFDEX 3D/DIE are integrated die structural analysis programs that accompany the respective BMF simulators, AFDEX 2D and AFDEX 3D. AFDEX MAT provides users with highly accurate true stress-strain curves for the materials in use at room or elevated temperature.
AFDEX 2D/3D allows combined 2D and 3D simulations to be carried out, and permits 2D results to be more vividly visualized via a powerful 3D computer graphic utility.
AFDEX DB provides material and process information, including flow stresses, forming machines, and the like. Flow stresses for most commercial materials are available with a wide range of state variables, including temperature, strain and strain-rate.
AFDEX Web is a special web version of the simulator that can be used online by small or large academic, commercial, and research communities.
Of course, all AFDEX developers are doing their best for AFDEX to satisfy the aforementioned requirements for intelligent MFS. In what follows, characteristics and typical applications of AFDEX are discussed in terms of its intelligence.
AFDEX is a general-purpose metal forming simulator, which meets the following requirements for intelligent bulk-metal- forming (BMF) simulation (BMFS)
AFDEX Application:
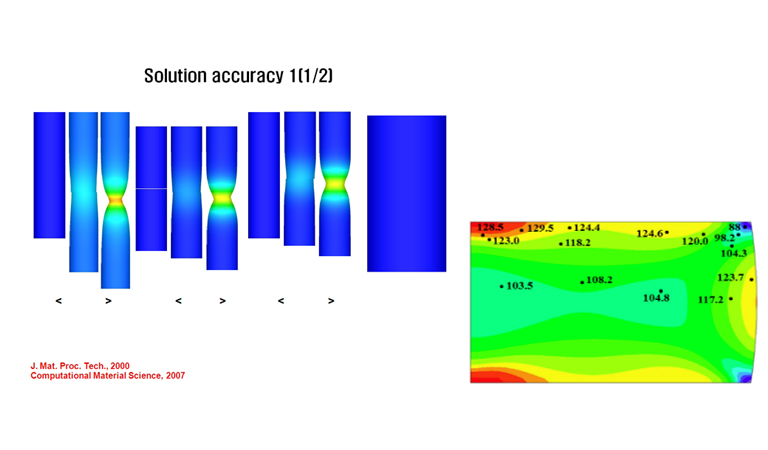
Material identifications
The program is based on the method for acquiring true stress-strain curves over large range of strains using engineering stress-strain curves obtained from a tensile test coupled with a finite element analysis. In the method, a tensile test is analyzed using a rigid-plastic finite element method combined with a perfect analysis model for its associated simple bar to provide the information of deformation.
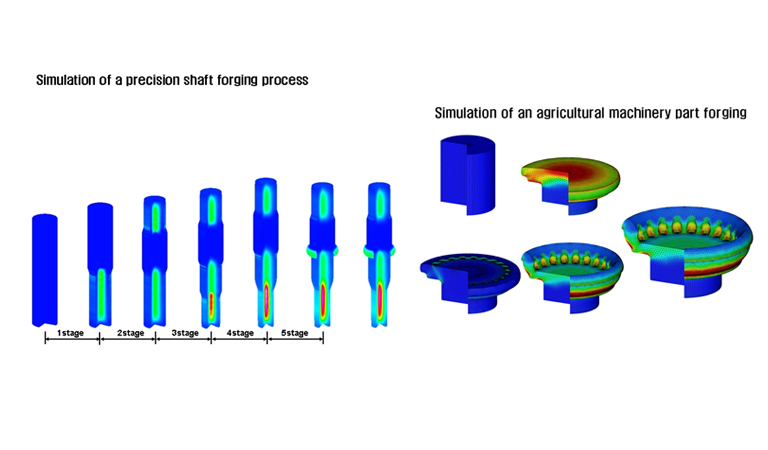
Conventional forging
With conventional forging, as the dies approach, the alloy plastically deforms and flows laterally touching the side walls of the die. The alloy continues to flow outside of the impression forming flash. a the flash thins it cools causing resistance to additional deformation. The cooled flash then adds pressure to the inside of the die cavity to promote metal flow into any design impressions that are unfilled.
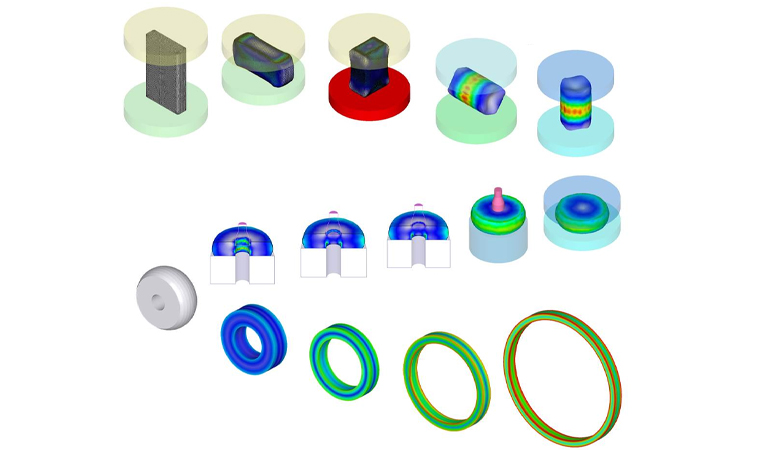
Incremental forming
The main advantage of incremental forming is that it is well suited for low cost prototyping or small batches of manufactured products. It can be used to create complex shapes with very simple tools. Because it is done with CAD/CAM the tool path can be created quickly and the changes are easy to apply. It can be done on any CNC milling machine or industrial robot, which also contributes to its cost-effectiveness.
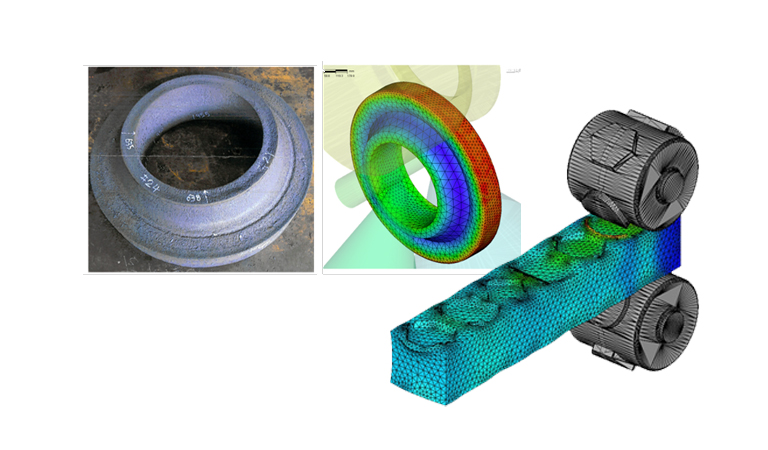
Rolling
Rolling involves passing metal between rollers to reduce the thickness of the material to a pre-determined size. The process utilizes a hammer and anvil or a drop hammer in larger machinery. Rolling can be achieved hot or cold. The cold method is often employed if the desired result is to toughen or harden the metal.
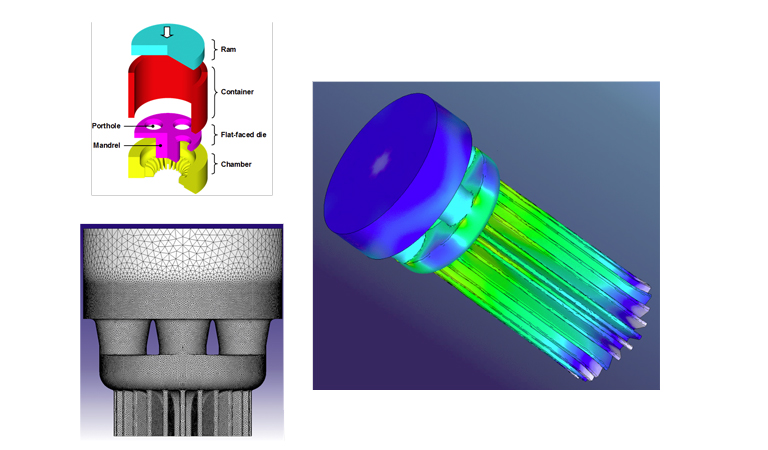
Extrusion and Drawing
When it comes to manufacturing, there are a variety of different methods that can be used. Two such processes are extrusion and drawing. Both of these processes have their own set of advantages and disadvantages, but when it comes to deciding which one is best for your project, it’s important to understand the differences between them.
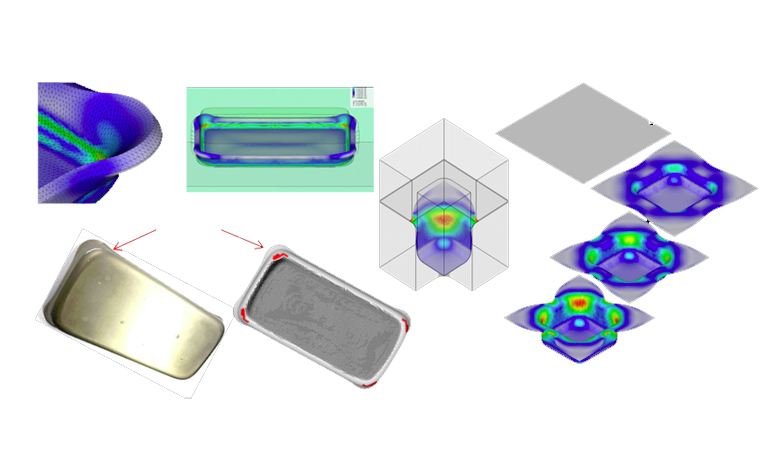
Sheet / Plate forming
Sheet metal forming involves manufacturing processes in which the shaping is carried out without changing the mass, volume and material composition. However, forming changes the surface and properties of the metals to be machined. The process involves clamping the ends of rolled metal sheet (usually thinner than 6 mm) and then stretching over a forming block to the desired shape.

Miscellaneous
Multi-body plastic deformation problems are hot issues in metal forming simulation. AFDEX started to be applied for several multi-body forming processes since last year. AFDEX V19 has experienced more complicated and actual processes than before. Fig. shows elastoplastic FE predictions of a forming process for assembling three parts. The comparison between 2D results and 3D ones shows good similarity.
Contact Us
SEND YOUR SUPPORT SERVICE REQUESTS ON BUSINESS TIMES AND DAYS, MONDAY TO FRIDAY